More With Less — Identify Waste (Pt. 1 of 3)
Improving agility by reducing waste can help do more with less.
Improving agility by reducing waste can help do more with less.
Key Takeaways
Waste is an indicator of inefficiency that hurts productivity and viability.
Work to find processes and products that require high effort and produce low value to identify waste.
Eliminate waste by automation, ownership, and utilizing talent.
Background
I’ve written about lean in a different context and on waste examples. However, I should have taken the time to write specifically about waste and how to identify it.
In this post, I will cover waste terminology (taken from the lean manufacturing methodology), signs to identify it, and the possible value of removing it.
What Is Waste
Waste, or the Japanese word for it, Muda, is an unnecessary allocation of resources that brings little to no value. Taiichi Ohno, the father of the Toyota Production System, covers eight types of waste in his book.
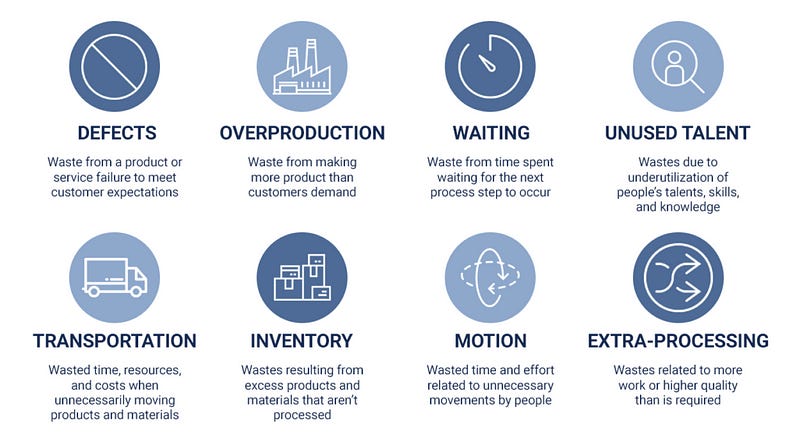
Some examples of waste in our everyday life include –
Short focus time between meetings — if I have 15 minutes between one session to another, I need more time for deep work, and the value from this time is limited (waiting).
Unutilized money sitting in the bank — can be considered waste without proper investment and saving (inventory).
Operation tasks for engineers — instead of innovating, engineers might work on operational tasks that require minimal skills (unused talent).
Perfecting a great solution — increasing code test coverage from 85% to 95% can create waste, or at least not as much value (extra processing).
How Can We Identify It?
With the definition and some examples in mind, let’s generalize the term waste and create clear signals to identify it. It all comes down to the simple ROI equation — value vs. effort.
If the effort invested in a specific process creates less value, some waste is involved, waiting to be eliminated. To identify it, we need to look for high-effort or low-value signals.
1 — Repetitive Tasks
Automate repetitive tasks to reduce the manual work involved. Abraham Lincoln once said, “Give me six hours to chop down a tree, and I will spend the first four sharpening the ax.” You should invest that much in automating manual processes.
2 — Ownership
When too many people are involved, work to remove unnecessary parts and increase ownership. The fewer people involved in a project, the more empowered they are. Extreme ownership is the favored form of leadership that yields the highest ROI in terms of waste.
3 — Underutilizing A Person’s Skills
Whether it’s low-effort tasks or low-value outcomes, find your way to work on tasks that requires your full attention and expertise. If you are not shining and crafting your skills, you’re likely engaged with a low ROI task.
Summary
Muda, or waste, is an indicator of inefficiency that hurts productivity and viability. There are different types of waste, which all, in their essence, indicate low ROI (investing more effort than the expected value).
You can eliminate waste by automating repetitive tasks, promoting extreme ownership while reducing dependencies, and utilizing talents and professional skills.